Ever wondered how everyday plastic items are made? The answer is in the complex injection moulding process. It’s used to make everything from household items to advanced medical devices. But what about making products with more than one material? How can we adjust the process for these complex designs?
The injection moulding process is key for making many plastic products. It’s vital for makers who want to make products with different materials. By learning about this process, you can bring your creative ideas to life.
Key Takeaways
- The THY Precision injection moulding process step by step includes clamping, injection, cooling, and ejection phases.
- For multi-material products, special techniques like overmolding and insert molding are needed.
- Knowing the benefits and uses of overmolding and insert molding helps in making smart manufacturing choices.
- Prototyping with these methods can solve problems and lead to a successful product.
- Multishot molding and picking the right equipment are key for quality multi-material products.
Understanding Overmolding and Insert Molding
When making products with different materials, overmolding and insert molding are key. These injection moulding process step by step methods combine various materials into one part. This opens up new design possibilities.
The Basics of Overmolding
Overmolding is a process where parts are molded together. First, a base is molded and then another layer is added on top. This makes a single solid piece. Overmolding works with many materials like thermoplastics and rubber.
Insert Molding: An Alternative Approach
Insert molding is similar but uses a pre-made base. Unlike overmolding, it adds a new part to an existing base. This method is great for adding plastic to metal or embedding electronics in thermoplastics.
Choosing the Right Manufacturing Method
Overmolding is good for products made of thermoplastics and/or rubber. It’s also for items with many layers and won’t be taken apart. Insert molding is better for using pre-made bases, especially metal or electronics, and making a single solid piece.
Overmolding | Insert Molding |
---|---|
Best for thermoplastics and/or rubber, multiple layers and materials, completed piece won’t need to be taken apart | Preferred for prefabricated substrates, metal or electronics substrates, finished part as one solid piece |
“Overmolding and insert molding are powerful tools in the world of multi-material products, allowing manufacturers to push the boundaries of design and functionality.”
Common Applications of Overmolding and Insert Molding
The injection moulding process step by step, overmolding, and insert molding are key in many industries. They make products from household items to medical devices. These methods are vital for designers and engineers because of their unique benefits.
Household and Consumer Products
Overmolding makes many household and consumer products, like toothbrushes and cell phone cases. It combines hard and soft materials well. Insert molding is great for making insulated pipes and embedding electronics in plastic.
Automotive and Transportation Industries
Automakers use insert molded and overmolded parts a lot. Insert molding is good for parts like electrical sensors and gears. Overmolding makes interior parts like door panels and handles look and work great.
Medical Devices and Equipment
Plastics are easy to sterilize, making them perfect for medical use. Insert molding makes pacemakers and cables. Overmolding is used for things like endoscopes, making them strong and smooth.
Industry | Overmolding Applications | Insert Molding Applications |
---|---|---|
Household and Consumer Products | Toothbrushes, cell phone cases, plastic furniture | Insulated pipes, wiring, electronic housings |
Automotive and Transportation | Interior components (door panels, handles, knobs) | Electrical sensors, gears, fasteners |
Medical Devices and Equipment | Endoscopes, colonoscopes | Pacemakers, defibrillators, medical cables |
As we keep looking for new and lasting products, the injection moulding process will stay crucial. Overmolding and insert molding will keep being key for making a wide range of products.
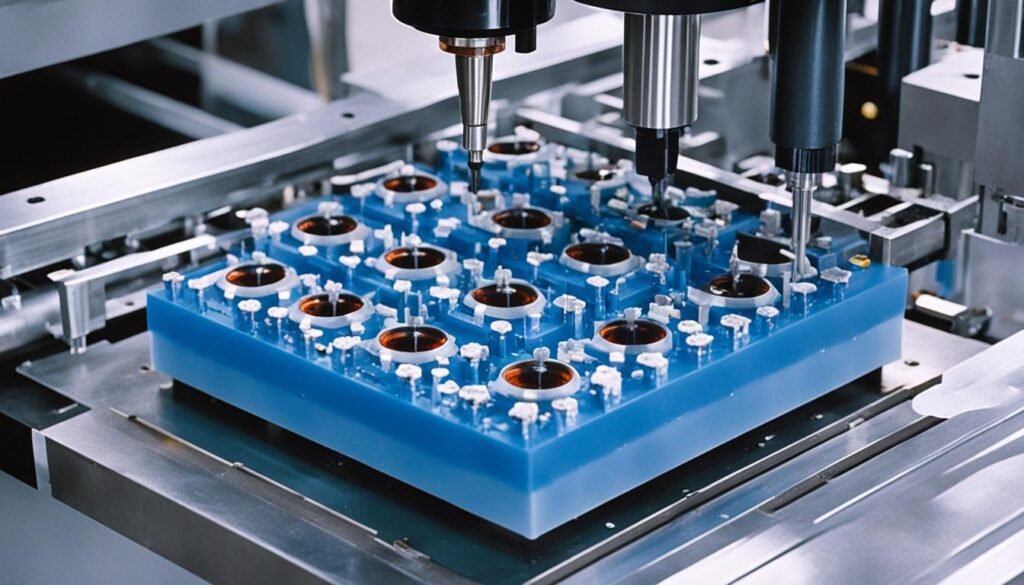
Prototyping with Overmolding and Insert Molding
The injection moulding process step by step is a powerful tool for product designers and engineers. Traditional prototyping can be tough and pricey. But, innovators are finding new ways to make it easier and cheaper by using 3D printed parts or molds for overmolding prototyping and insert molding prototyping.
Unlocking the Potential of 3D Printed Molds
Using 3D printed molds for the injection moulding process step by step has a big advantage. It lets product designers and engineers quickly and affordably make custom prototypes. This helps them test ideas and fix any problems fast, saving time and money.
With 3D printed molds, companies can quickly try out different designs. They can make many versions and improve the product before making it on a large scale. This quick way of working lets them get new products to market faster, staying ahead of others.
“Prototyping can be challenging and expensive, but innovators are overcoming this by using 3D printed parts or molds for overmolding and insert molding. This saves time and money during the prototyping phase, allowing product designers and engineers to test concepts and troubleshoot design elements more efficiently.”
Embracing the Power of Overmolding and Insert Molding
Product designers and engineers are also looking into overmolding prototyping and insert molding prototyping. These methods let them make complex products with different materials. This helps them test and improve the product during the early stages.
By using overmolding or insert molding, innovators can make prototypes that are very close to the final product. This gives them important insights and feedback as they work on the product.
Creating custom prototypes quickly and affordably with 3D printed molds, overmolding, and insert molding is changing how product designers and engineers work. This new way lets them bring innovative products to market faster. It helps them stay ahead and make customers happy with new solutions.
Injection Moulding Process Step by Step for Multi-Material Products
The injection moulding process step by step for multishot injection moulding combines two or more resins in one process. This method adds value by enabling soft-touch features, better performance, permanent designs, and assembling parts in the mold. It’s a powerful way to make plastic products better.
Even though multishot injection moulding is established, it’s not used everywhere. To use it, manufacturers need to think about the multishot tooling and multishot equipment needed for the process.
Multishot Molding: Adding Value to Plastic Products
Multishot or multi-component molding lets manufacturers mix different materials in one molding cycle. This technique is great for making a variety of innovative products. From soft-touch grips to parts that work better and look good, it’s versatile.
Using different resins, manufacturers can tailor plastic products for specific needs. The injection moulding process step by step for multishot molding opens up new design and efficiency possibilities. It’s not something you can do with just one material.
Multishot Tooling and Equipment Selection
Multishot molds need special design and building to handle multiple materials. There are three ways to make space for the first and second shots: using a rotary platen, changing the core and cavity steel, or using a core toggle.
Choosing the right multishot injection molding machine is key. Things like lead time, capacity, and cost matter a lot. Working with experts and planning well is crucial for success.
Multishot Molding Technique | Description |
---|---|
Common Core Using Rotary Platen | Uses a rotating platen to position the common core between the first and second shots, allowing for the injection of different materials. |
Core and Cavity Steel Change | Involves physically changing the core and cavity steel to accommodate the second shot, providing more design flexibility. |
Core Toggle | Uses a toggle mechanism to move the core in and out of the cavity, enabling the injection of multiple materials in a single cycle. |
Regardless of the injection moulding process step by step used, multishot molding needs careful planning, special equipment, and teamwork. Designers, engineers, and production teams must work together to get the desired results.
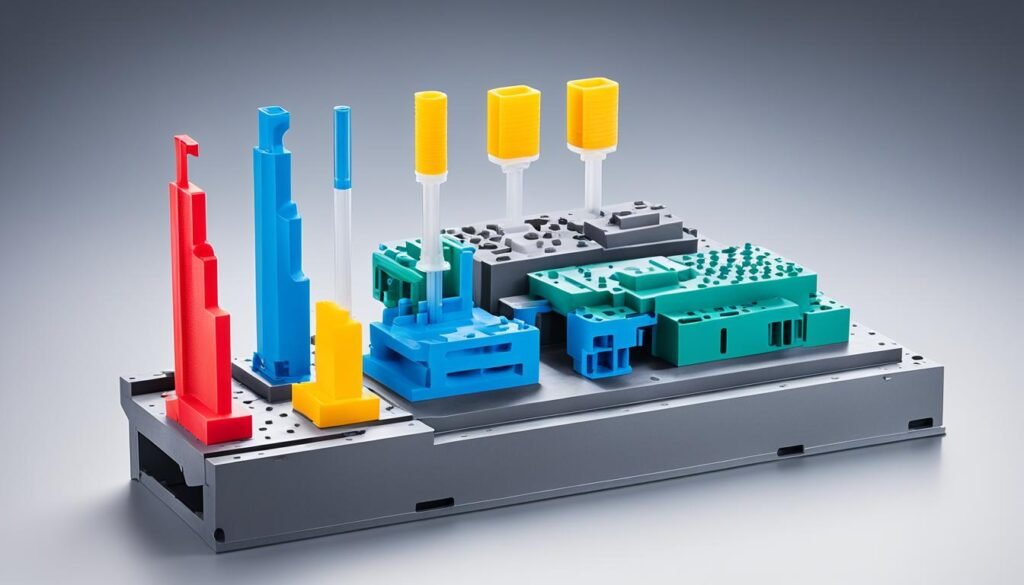
The Injection Moulding Cycle
The injection molding process is key for making many products, from everyday items to car parts. At THY Precision, we know how vital it is to get the injection moulding process step by step right. This ensures we make parts that are strong, long-lasting, and affordable. Let’s look at the main stages of the injection molding cycle.
Clamping and Injection Steps
The injection moulding process step by step starts with clamping. Here, the mold’s two halves are closed tightly by the clamping unit. This makes sure the molten plastic can be injected without leaking.
Then, the injection phase happens. The molten plastic goes through the sprue system and fills the mold cavity. It takes the shape of the part being made.
Cooling and Ejection Phases
After injection, the plastic starts to cool and harden. When it’s fully cooled, the mold opens, and the part comes out using the ejector system. This last step in the injection moulding process step by step gets the finished part ready for the next step or packaging.
At THY Precision, we’ve got the injection moulding process step by step down to a science. Our top-notch equipment and skilled team make sure we deliver parts that meet our clients’ high standards. We’re known for our consistent and reliable results.
Conclusion
The injection moulding process is a key way to make products with different materials. THY Precision is an expert in overmolding, insert molding, and multishot molding. They help you make innovative, high-quality items for many industries.
Learning about the injection moulding process lets you explore new possibilities for your products. You can make everything from household items to car parts to medical devices. These methods offer flexibility and precision, making your ideas come to life with great quality and speed.
Working with THY Precision, a top name in injection moulding, gives you the support you need. They are dedicated to innovation and making customers happy. They ensure your projects go smoothly, from the first prototype to large-scale production.